Does the seemingly subtle undulation in a sheet of glass hold secrets that impact its clarity and performance? The answer, as we delve into the world of "roller wave," is a resounding yes, and understanding this phenomenon is critical for anyone involved in the production, specification, or use of flat glass.
Often unnoticed by the casual observer, roller wave is a form of optical distortion that arises during the manufacturing process of flat glass. It manifests as a subtle waviness, a rippling effect across the surface of the glass. While seemingly minor, this distortion can have significant consequences, affecting everything from the aesthetics of a building facade to the accuracy of optical instruments.
The term "roller wave" itself is a key indicator. It points to the very heart of the problem: the process by which glass is formed. The journey begins as molten glass is poured onto a bed of rollers within a massive furnace. As the glass travels through this intense heat, it gradually transforms into a solid sheet. This, however, is where the potential for imperfection arises.
During this critical heating process, the glass travels through the furnace on ceramic rollers. While traveling, the heated glass can slightly sag between rollers, causing the characteristic roller wave distortion. The degree of this sag, and thus the severity of the wave, depends on several factors, including the glass's thickness, the distance between the rollers, and the temperature profile within the furnace. It's a delicate dance between heat, gravity, and the mechanical support provided by the rollers.
The roller wave is most easily identified when viewing the glass by the reflection of rectilinear images from the outside of a building in which it is installed. The ends of each piece of glass tend to sag to a greater degree due to the cantilever effect of the unsupported ends of glass at the leading and trailing edges; this sag is known as 'edge'.
Consider the challenges for the Honda enthusiasts: We've spared no expense to bring Honda enthusiasts the very finest specialty pistons available anywhere for both normally aspirated, supercharged, and turbocharged.
After the heating phase, the glass then passes through the "quench," a rapid cooling process designed to solidify the glass and impart its final characteristics. This rapid cooling can further impact the roller wave, potentially exacerbating or even mitigating the distortion depending on the specifics of the process.
Understanding roller wave requires a grasp of the intricacies of glass manufacturing. It's a process that blends art and science, where minute variations in temperature, pressure, and mechanical support can have profound effects on the final product. While roller wave is often described as an "optical distortion," it's not merely a cosmetic issue.
The optical properties of glass are critical for many applications. In architectural settings, distorted glass can alter the visual appearance of a building, affecting its aesthetics and potentially impacting the quality of views. In scientific and technological applications, even minor distortions can interfere with precision measurements, impacting the accuracy of optical instruments and the performance of high-tech equipment.
The good news is that roller wave can be managed and minimized. Manufacturers employ a range of techniques to mitigate its effects. Precise control over furnace temperatures, roller spacing, and cooling rates are all essential. Innovations in glass manufacturing technologies, such as advanced furnace designs and improved roller materials, have further reduced the prevalence and severity of roller wave.
The goal is not necessarily to eliminate roller wave entirely, as some degree of distortion is often unavoidable. Instead, manufacturers strive to control it, keeping it within acceptable tolerances. The glass association of north america (gana) publications, for example, specify allowable tolerances for surface distortion, including roller wave height.
Typical roller wave height is measured within a range of 0.002 to 0.005 inches (0.05 to 0.13 mm), depending on the glass thickness. By adhering to these standards, manufacturers can ensure that their products meet the required performance criteria, preventing that the imperfections do not compromise the intended functionality of the glass.
It is important to emphasize that roller wave distortion is a normal part of the process.
Consider the opportunity, "Summer camp spots are available! Jil's is a safe, clean, fun, learning environment for students ages 5 yrs through 12 yrs old. Call today to book your child's spot now!"
But what are the implications for other applications? Roller wave can be especially problematic in applications where pristine optical clarity is paramount. For example, in the construction of telescope lenses, or in the production of high-precision display screens, roller wave can significantly compromise image quality.
In the broader architectural context, roller wave can affect the way light interacts with a building's facade. As light passes through distorted glass, it can be refracted and scattered, creating visual distortions. This is more noticeable with larger glass panels and when viewing reflections on the glass surface. In some cases, this distortion may be undesirable, while in others, it can add an interesting visual character to a building.
The concept of roller wave extends beyond aesthetics. It's a window (no pun intended) into the complex world of materials science and manufacturing technology. The glass industry is constantly working on improving its processes and technologies to deliver high-quality glass products. A key part of that work is to understand and manage the phenomenon of roller wave.
Consider the advantages: "We provide a traveling pop up roller skating experience for an admission fee and an optional skate rental charge."
The roller wave will host family programming, skating lessons, wellness events, and more through june 4, 2023. The space is open wednesday and thursday from 12:00pm to 10:00pm and friday through.
Consider the advantage: The waveroller is a perfect companion to our category leading theragun percussion massage guns.
Key Aspect | Details |
---|---|
Definition | Optical distortion in flat glass. |
Cause | Glass sagging between rollers during the heating process in a furnace. |
Impact | Affects visual clarity, particularly when reflecting rectilinear images. |
Measurement | Wave height typically ranges from 0.002 to 0.005 inches (0.05 to 0.13 mm). |
Control | Controlled through precise furnace temperature control, roller spacing, and cooling rates. |
Standards | Adhering to tolerances specified by organizations like GANA. |
Importance | Critical for both aesthetics and functionality in various applications. |
The space is open wednesday and thursday from 12:00pm to 10:00pm and friday through.
Roller wave is a common form of this optical distortion.
During the heating process, the glass travels through the furnace on ceramic rollers, while traveling, the heated glass can slightly sag between rollers causing roller wave distortion. Mark abbott & john madocks applied process technologies, inc.
The glass then passes through the quench, rapidly cooling the glass after the heating process. This article delves into the reasons behind roller wave and offers practical steps to minimize it. Understanding roller wave...
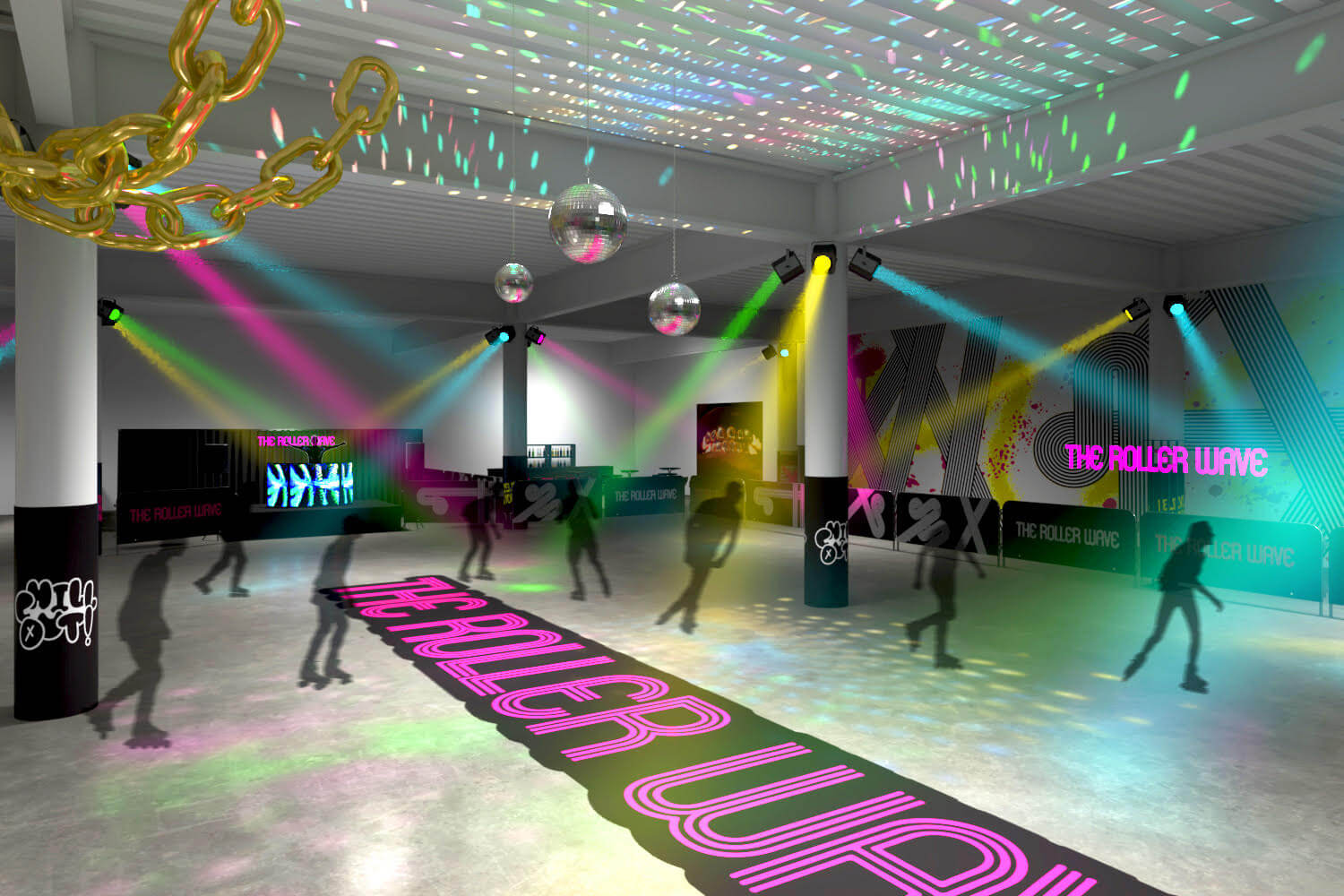

